ARCELORMITTAL HAMBURG IS THE FIRST GREEN STEEL MILL
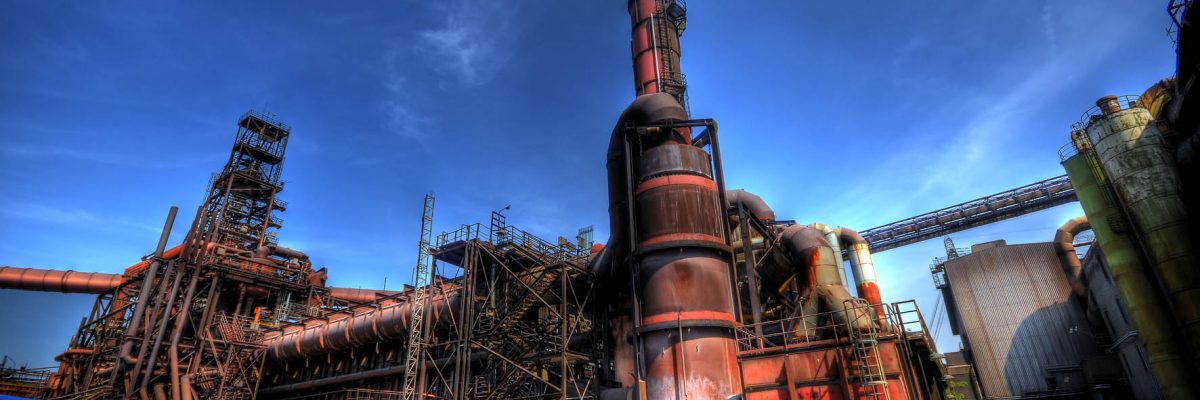
ArcelorMittal is developing an innovative new project at its Hamburg, Germany, facility aimed at the first commercial production and use of steel prepared with 100% hydrogen as a reducing agent, with an annual production capacity of 100,000 tons of steel.
Last year, ArcelorMittal announced it had signed a cooperation agreement with Midrex Technologies to design a demonstration plant in Hamburg and work on a number of related research and innovation projects.
“We are working with a world-class supplier, Midrex Technologies, to learn how we can produce green pig iron to produce steel on a large scale using only hydrogen. This project, combined with our ongoing carbon use and sequestration projects, is key to achieving a carbon-neutral balance in Europe by 2050. However, how quickly the transformation happens will depend on the political environment,” said Carl de Mare, ArcelorMittal’s vice president responsible for technology strategy.
ArcelorMittal Hamburg already produces steel using DRI technology. During the process, iron oxide pellets are reduced to metallic iron, the raw material for high-quality steel production, by extracting oxygen using natural gas.
“Our plant is the most energy-efficient production facility at ArcelorMittal,” says Dr. Uwe Braun, CEO of ArcelorMittal Hamburg, adding that the existing Midrex plant in Hamburg is also the plant with the lowest CO2 emissions for high-quality steel production in Europe.
“With the new hydrogen-based direct reduction iron plant that we are now planning, we will take steel production to a whole new level, which is part of our pan-European ambition to achieve carbon-neutral balance by 2050,” Dr. Brown concludes.